7 min read
Inefficient Asset Utilization Costs Construction Companies
By: Elizabeth Sholes on Mar 1, 2021 11:00:00 AM
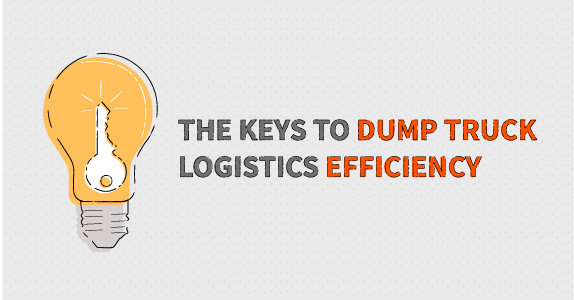
What is fixed asset utilization? When it comes to managing construction logistics, ensuring your fleet assets are fully utilized is a great place to start. Many construction companies assume that because their dump trucks are out on the road for a portion of the day that they are making the most out of those assets. However, in this article, we will explore how that mentality may be costing your construction company in the long run.
Learning how to improve fleet asset utilization is just one component of a successful logistics operation. If you are interested in learning about other levers, like dispatch management, you can pull to increase dump truck efficiency, check out the remainder of this series.
For now, let’s focus on maximizing your profits. This includes understanding equipment ratios, being able to react more quickly to fully leverage your assets, and investigating ways that technology can help your team stay organized - while making the most of your fixed assets.
Increase asset utilization to Maximize Your Profits
Regardless of how many dump trucks your construction company owns, increasing asset utilization is a cornerstone of a successful logistics operation. It is not enough to have your trucks out on the road for a portion of the day. In fact, every hour your trucks are not on the road, at an acceptable rate, is an hour that asset depreciates without any revenue.
Most construction professionals would readily agree with the statement above, but what does it really mean for your business and how can you measure it?
Let’s take a step back and define asset utilization. Then we can take a closer look at what asset utilization ratios measure. Finally, we can explore how you can start to assess your current asset utilization and even improve your asset utilization ratios.
Definition & Formula:
Asset Utilization Ratio: Asset utilization ratio calculates the total revenue earned for every dollar of assets a company owns.
Asset Utilization Formula: Asset Utilization = Revenue / Average Total Assets
What does this mean? Well, if a company has an asset utilization ratio of 44%, that company earned $.44 for each dollar of assets held by the company. When you focus on increasing asset utilization, you are committing to an effort to be more efficient with each dollar of assets your company owns. By using this formula, you can compare your company’s efficiency over time.
What are Equipment Ratios and How Do They Impact Asset Utilization?
Now, let’s explore how to assess the utilization of assets for your construction company. We like thinking about it in this framework of equipment ratios:
Deployment: The time a dump truck or piece of equipment is on-site and expected to work, as a percentage of the total ownership period.
Availability: The time a dump truck or piece of equipment is on-site and able to work as a percentage of the time a machine is on-site
Utilization: The time a dump truck or piece of equipment is actually working on-site expressed as a percentage of the time the machine is on-site and able to work.
Deployment has typically been represented by weeks per year. Taking the number of weeks per year as an asset is deployed and multiplying by x 40 (hours per week) helps determine the total number of hours it takes to recover the fixed costs of owning that piece of equipment. Ask yourself...how many hours does a dump truck need to work before it has paid for itself?
The time that you own an asset but it is not deployed is wasted time. Essentially, you are paying for that equipment and you aren’t making any money off it when it isn’t being used.
Simply knowing this information doesn’t change anything. Knowledge can help force your organization to think about whether it should be selling any pieces of equipment - but it does little to improve asset utilization.
We challenge you to take a more detailed view of deployment. Hone in on how many hours per week that piece of equipment is deployed. Think proactively about whether or not your company is in the position to either increase the number of projects it takes on to fully leverage owned assets - or - whether you should look for opportunities to subcontract your dump trucks out when project schedules are light. Remember, you own the asset 24/7, which means that if you aren’t currently looking at opportunities like night-time work you are missing out on 12 potential deployment hours!
This level of granularity is often difficult to ascertain without outside help. Logistics platforms are now able to help construction companies by providing the data needed to track this information. Furthermore, since some trucking logistics platforms, like TRUX, offer all-in-one solutions, you can also subcontract your trucks directly through the platform.
Availability is the time that machines are deployed on-site and expected to work. However, there are two instances where availability is impacted. The first asset utilization example occurs when trucks are on the job and a mechanical breakdown happens. The impacts of this are easily felt and understood by the entire team - mechanical breakdowns put construction projects and timelines at risk. Measuring this type of occurrence can help you identify whether your preventative maintenance plan needs improvement or whether your fleet is aging out of effective and reliable work. The second type of instance is when the machine is able to work but is off shift and not required to work. In this scenario, your organization may benefit from subcontracting that vehicle out.
Utilization is the amount of time machines are actually working on-site. It is important to note that there can still be wasted time with machines that fall into this category. The type of waste that occurs at this level is frustrating because it means that the machine has been deployed, is on-site, is able to work - and isn’t working. This could be the time that a dump truck spends waiting in line at a job site or quarry. It could also be the time that they wait while the jobsite crews get ready for them.
It is in this area of waste that logistics platforms really prove their value. Because you can plan, schedule, and dispatch more efficiently, you see efficiency gains at the jobsite resulting in less construction equipment utilization waste.
React More Quickly to The Needs of Your Organization
Now that we have a better understanding of what asset utilization is and the equipment ratios you can leverage to track asset utilization, it is time to think about what to do with your asset utilization ratio analysis. Monitoring this is a great first step but taking action is necessary to improve your asset utilization and efficiency.
The easiest way to begin to impact overall asset utilization is to start with the wasted time that occurs with machines that are working on-site but are underutilized. What changes can your organization make to ensure that dump trucks that are on-site or en route are performing to their full capacity?
It starts with better scheduling and is reinforced by better communication. For example, what would happen to jobsite efficiency if dispatchers were able to stagger dump truck arrival times by 15 minutes? That one small change could mean that you get hours of utilization back - simply because dump trucks won’t be waiting in line to drop off or pick up material.
With 5 trucks running for a full day’s worth of work, that could mean you get an additional hour of usable time per truck per day.
Better communication between the jobsite and dispatch reinforces these changes. If things are progressing slower or more quickly on a jobsite than anticipated, jobsite contacts can relay that information back to dispatch. With the appropriate tools in place, dispatch can adjust trucking volume to the jobsite to accommodate - reducing the wasted time even further.
Now that you have addressed the easiest problem to solve. Let’s take a closer look at a more complex challenge. What if the assets you own aren’t appropriately matched to the number of projects you have taken on?
If you have more projects and need to increase trucking volume, is it best to purchase an additional fixed asset or would it be ideal to sub the work out to a hired truck? In many cases, the flexibility that hiring trucks for a shorter period of time is beneficial. You can turn to a broker, independent owner-operators, or a fleet of trucks. But that takes time and we are trying to make you more efficient - not inefficient.
Alternatively, you may have a slower month where the trucks you own aren’t needed for your own projects. What about subcontracting them out to ensure they are still earning for you - even if you don’t have a heavy project schedule at the moment? This can be ideal for many construction companies but it does require additional legwork and scheduling to accomplish.
Logistics platforms help companies find the trucks they need, when they need them, and allow contractors to find additional work for their trucks when their own project schedule is light. Not to mention the built-in tools to help track trucks and optimize scheduling and dispatch.
Use A Logistics Platform to Improve Asset Utilization
You may be able to find a simple asset utilization ratio calculator online but that will only be as good as the inputs you are able to provide. Simple calculators may help you get a better baseline understanding of where your asset utilization falls today but it will not provide you the tools you need to make meaningful changes to asset utilization over time.
Leveraging a logistics platform, like TRUX, is a great way to ensure your team has the tools they need to be successful at improving asset utilization. Poor utilization costs construction companies money. Logistics platforms help ensure that your fleet of trucks stays deployed and active. They also provide your team with the practical tools needed to implement changes over time. If you need help creating your plan, download our FREE guide and see big changes in the next three months.
Understanding equipment ratios, being able to react more quickly to fully leverage your assets, and using technology to help your team can help you make the most of your fixed assets. If you are interested in learning more about how logistics platforms are helping construction companies create better fleet asset utilization, schedule a call with one of our logistics specialists today.
Related Posts
Importance of Tracking Asset Utilization for Fleet of Dump Trucks
When you look at your fleet of dump trucks, do you see them as half full or half empty? It’s not a...
A Digital Marketplace and Apps for Dump Truck Fleet Owners | Trux
Summer’s here, no doubt about it. All across the country, it’s hot--and we’re not just talking...
How Dump Truck Company Logistics Software Creates Efficiency
Over the course of the next five weeks, we will be exploring a series of topics to help...