9 min read
How Smarter Hauler Management Helps You Do More with the Trucks You Already Have
By: TRUX Team on Apr 11, 2025 11:00:00 AM
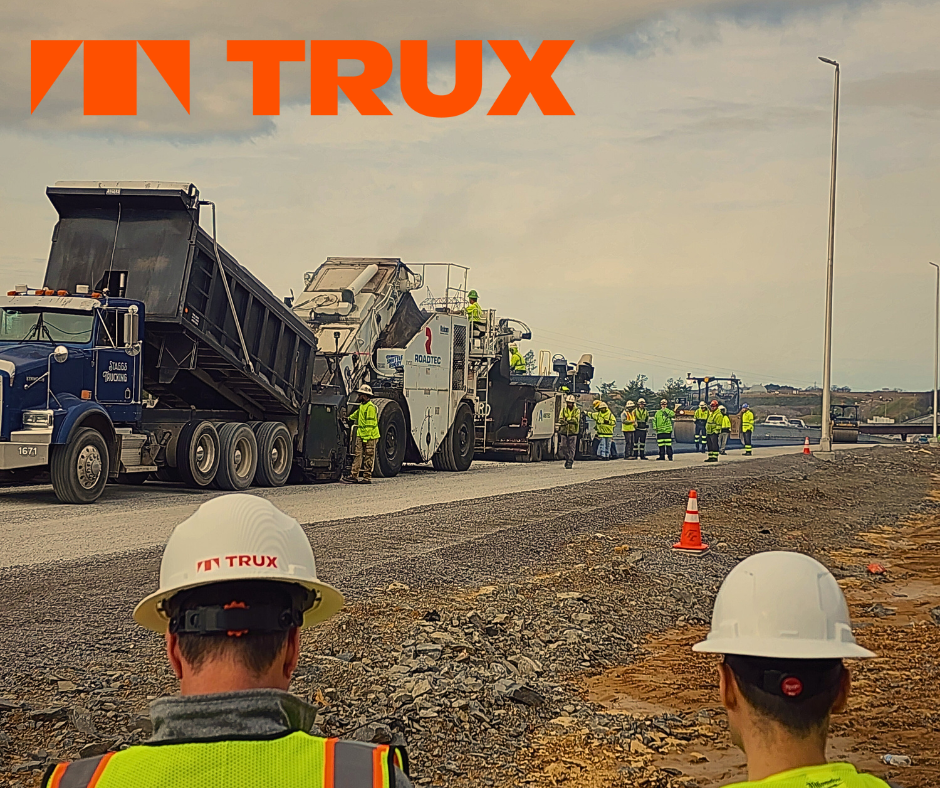
Think you need more trucks to move more material? Not necessarily.
In today’s environment, trucking capacity isn’t always easy to come by. Between rising demand, driver shortages, and unpredictable schedules, finding reliable haulers, especially on short notice, has become a real challenge. If you’re only relying on adding more trucks to increase output, you’re fighting an uphill battle.
The reality is this: most contractors and material producers already have enough haulers, they’re just not getting the most out of them.
Outdated systems like whiteboards, spreadsheets, and endless phone calls create inefficiencies that add up fast. Trucks sit idle, schedules fall apart, and materials don’t get delivered on time. Not only are these inefficiencies costing you money, they’re also costing you revenue. Every missed load or delayed delivery is money left on the table.
The good news? With the right technology in place, you can start using the trucks you already have more effectively. Trux gives you the tools to manage both internal and third-party haulers in real-time, so you can eliminate waste, reduce downtime, and maximize every shift.
Click a topic below to jump to the relevant section:
The Real Bottleneck Isn’t Capacity, It’s Visibility
How Manual Scheduling Is Holding You Back
Technology Gives You a Full Picture, In Real Time
Smarter Scheduling = More Loads Moved Per Day
Only Pay for What’s Done, Not What Was Scheduled
Real Results from Smarter Hauler Management
You Don’t Need More Trucks, Just Better Tools
The Real Bottleneck Isn’t Capacity, It’s Visibility
A lot of teams think they need more trucks to get the job done faster. But the truth is, without real-time visibility, even the best fleet won’t perform at its peak. You can’t manage what you can’t see, and that’s where most operations start falling behind.
Right now, many contractors and material producers are dispatching haulers with limited or no insight into what’s actually happening on the ground. You might know who was scheduled to show up, but do you know who actually did? Do you know how long they waited at the plant? How many loads they’ve completed so far? If a truck breaks down or a hauler is running late, how quickly can you pivot?
This lack of visibility causes bottlenecks that slow everything down, from the job site to the back office. Trucks end up idling, crews stand around waiting for material, and dispatchers scramble to keep things moving. And every minute of confusion or delay is money going out the door.
Technology like Trux solves this problem by giving you real-time insight into every hauler’s location, status, and performance, whether they’re part of your own fleet or a hired truck. With live tracking and digital load slips, you’ll finally have a full picture of your operations so you can make faster, smarter decisions and keep your jobs running on schedule.
How Manual Scheduling Is Holding You Back
If you're still relying on calls, texts, or spreadsheets to schedule your haulers, you're not alone, but you’re definitely working harder than you need to be. Manual scheduling is one of the biggest time-wasters in the industry, and it’s quietly limiting how much work your team can actually get done.
Coordinating haulers by phone leaves too much room for miscommunication. Job details get lost in the shuffle, last-minute changes cause confusion, and haulers often don’t have the full picture when they roll out. Worse, when something does go wrong, like a breakdown, delay, or site issue, dispatchers have no easy way to update the plan. They’re left scrambling to play catch-up while the job keeps falling further behind.
The problem gets even bigger when you're juggling both internal trucks and third-party haulers. Keeping track of who's assigned where, who showed up, and who's falling behind is nearly impossible without a centralized system.
Every delay means fewer loads moved, higher labor costs, and frustrated crews. And at the end of the day, your ability to hit project deadlines, and make a profit, depends on how well you can manage that schedule.
This is exactly where platforms like Trux change the game. With drag-and-drop dispatching, real-time updates, and automated hauler communication, your team can react fast, adjust on the fly, and keep jobs running smoothly without blowing up everyone’s phone. It’s not just easier, it’s a smarter way to run your operation.
Technology Gives You a Full Picture, In Real Time
When you're managing dozens of moving parts, trucks, jobs, haulers, and crews, you need more than a calendar and a phone to keep it all under control. That’s where real-time technology makes all the difference.
With Trux, you don’t have to wonder where your trucks are or how a job is progressing. You get a live, digital window into every active hauler, whether they’re part of your company fleet or brought in through a third party. You’ll see truck locations, load counts, shift progress, and even how much material has been delivered, all from a single platform.
That kind of visibility isn't just convenient, it’s powerful. When something changes, like a delay at the plant or an urgent load needed on another site, you can respond immediately. No more guesswork, no more blind decisions. You’re working with real data, in real time.
Trux also provides digital load slips and shift validation, so you know exactly when haulers start, stop, and how much work was actually completed. That means no more chasing down paperwork, no more billing disputes, and no more paying for time that wasn’t worked.
In short: technology doesn’t just show you what’s happening, it gives you the control to take action before small problems turn into big ones.
Smarter Scheduling = More Loads Moved Per Day
Let’s face it, every delay on the schedule is a missed opportunity. If your haulers are waiting around for assignments or sitting idle between loads, you’re losing both time and money. And the worst part? It’s preventable.
With smarter scheduling tools, you can make sure every truck is being used to its full potential. Trux lets you assign and adjust hauler schedules in seconds with a simple drag-and-drop system. If something changes on the job, like weather, a delay at the plant, or a last-minute load, you can instantly notify all haulers involved. No more calling down a list. No more crossed wires. Just fast, clear updates that keep the job moving.
When your team can react in real time, you reduce idle time, improve truck turnaround at the plant or site, and keep your haulers productive throughout the day. That’s how you get more loads moved, with the same number of trucks.
It’s not about pushing your team harder. It’s about giving them better tools to work smarter. And when you do that, everything flows better, material gets delivered faster, job sites stay on schedule, and your bottom line gets a healthy boost.
Only Pay for What’s Done, Not What Was Scheduled
In the dump truck world, time is money, and overpaying for time not worked adds up fast. If you’re relying on paper timecards or verbal shift confirmations, there’s a good chance you’re paying for idle time, no-shows, or incomplete work without even realizing it.
That’s where Trux takes a smarter approach. With geofencing and digital shift validation, you get a crystal-clear view of when haulers arrive at the plant, when they leave the job site, and everything in between. This automated tracking means no more guessing, no more chasing down timesheets, and no more “he said, she said” about whether a shift was fully completed.
Here’s what that really means for your business:
- You only pay for actual work performed, not scheduled hours or time spent idling.
- You eliminate unauthorized overtime and shift overages.
- You have clean, digital records that make invoicing and reconciliation painless.
This isn’t just about cutting costs, though you’ll definitely see savings. It’s also about taking back control. When you know exactly what you're paying for, you can plan jobs more accurately, negotiate smarter contracts, and run a tighter, more profitable operation.
Bottom line: if you're still trusting paper logs or word-of-mouth to manage hauler pay, you're leaving money on the table. Trux helps you keep that money where it belongs, in your pocket.
Real Results from Smarter Hauler Management
When you start using technology to manage your haulers more effectively, the impact goes beyond just a smoother day on the job site. You start to see measurable improvements across your entire operation, faster deliveries, lower costs, and a more productive team.
Contractors and material producers using Trux are seeing results like:
- 15–20% improvement in plant and site turnaround times
Less waiting around means more material moved and more work done per day. - 7–10% increase in material delivered annually
By reducing downtime and tightening up dispatch, you’re able to complete more loads without adding more trucks or drivers. - 18% boost in dispatcher productivity
With less time spent on phone calls, paperwork, and schedule juggling, your team can focus on what actually moves the needle.
These aren’t just feel-good numbers. They represent real dollars saved, and more importantly, dollars earned that would’ve been lost without tighter control over hauling operations.
Whether you’re looking to hit tighter deadlines, stretch your resources further, or simply stop burning cash on inefficiencies, smarter hauler management with Trux delivers results you can see in your bottom line.
You Don’t Need More Trucks, Just Better Tools
If you’ve been feeling the pressure to find more trucks, you’re not alone. But here’s the truth: most operations don’t have a truck shortage problem, they have an efficiency problem. The trucks are there. The drivers are ready. But without the right systems in place, you’re stuck running at half capacity.
Every time a truck sits idle, a load is missed, or a hauler’s time isn’t accurately tracked, money is walking right off the job site. That’s money in fuel, wages, delays, and, most importantly, missed opportunity.
With Trux, you don’t need to scramble for more trucks. You just need to get more out of the ones you’re already using. Whether it’s your own fleet or third-party haulers, Trux gives you the visibility, control, and flexibility to run a tighter, more profitable operation.
Still running your hauling the old-school way?
Let us show you how smarter scheduling, real-time tracking, and digital shift validation can help you move more material without adding more trucks.
👉 Schedule a quick demo and see how Trux helps you take full control of your hauling