9 min read
Reducing Downtime: Best Practices for Hauling Operations
By: TRUX Team on Apr 4, 2025 9:13:32 AM
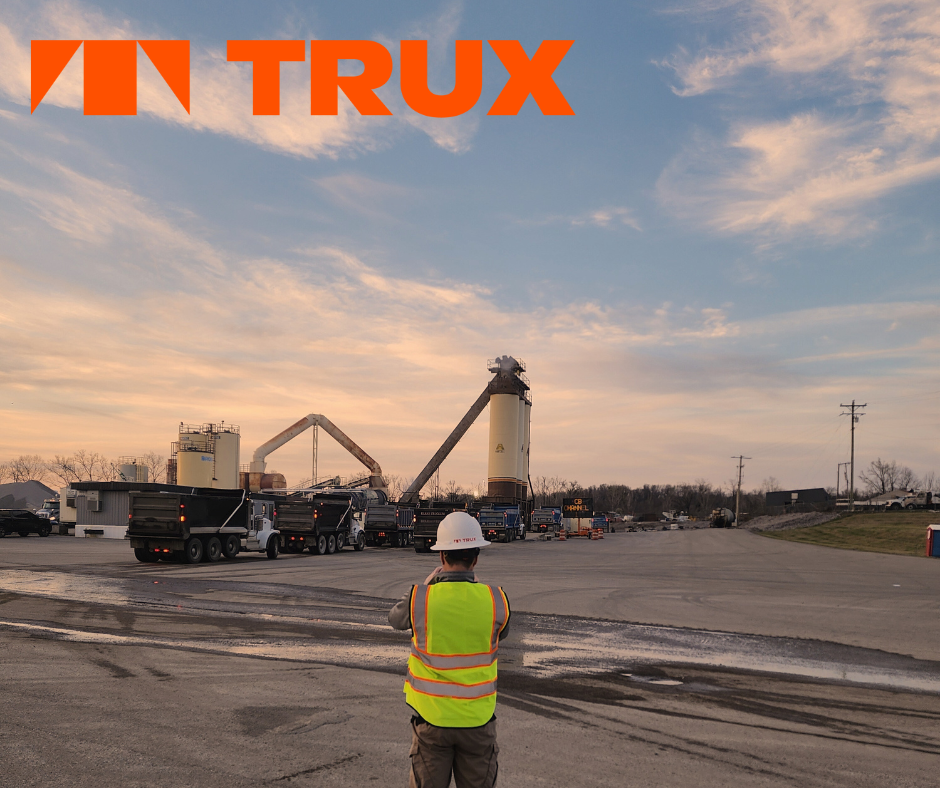
When your operation relies on steady material movement, downtime isn't just an inconvenience—it’s a drain on time, resources, and revenue. Whether it's trucks stuck in the yard, drivers waiting on site, or dispatch teams bogged down with calls and paperwork, every delay eats into your productivity.
The good news? Most of that downtime is preventable.
With the right tools and a few smart adjustments, material producers can streamline hauling operations, reduce turnaround times, and get more done with fewer headaches. Here's how—and why platforms like Trux Materials are leading that shift.
Click a topic below to jump to the relevant section:
The Hidden Cost of Idle Trucks
5 Ways to Cut Downtime and Keep Deliveries Moving
Trux Materials: Purpose-Built to Eliminate Downtime
Start Running Tighter, Smarter Hauls
The Hidden Cost of Idle Trucks
Downtime isn’t always obvious. A few minutes of waiting here, a slow turnaround there—it adds up quietly. But over the course of a day, those small delays can keep a truck from making an additional delivery. And that’s where it starts to cost you.
With Trux Materials, many producers are able to get one extra load per truck, per day—without adding more trucks or staff. That’s not a theoretical benefit—it’s what happens when you remove the friction from dispatching, reduce wait times, and give your team real-time visibility into every load.
If you’re running 10 trucks, that’s 10 more loads moved daily. Over the course of a week, you’re looking at 50 additional deliveries—without increasing your overhead.
More loads moved equals more material delivered, more revenue generated, and more value out of the trucks you already own or hire.
What’s Slowing You Down?
Downtime isn’t just a random occurrence—it’s the result of small breakdowns across your operation that stack up fast. The problem is, most producers are too busy trying to keep up with day-to-day demands to step back and spot the patterns.
Here are the most common causes we see on jobsites and at the plant:
1. Outdated Dispatch Systems
Manual dispatching is still the norm for many teams. Whether it’s a whiteboard in the office or a spreadsheet that gets emailed out, these methods leave too much room for human error. When haulers don’t get updates on time—or worse, get the wrong ones—loads get missed, trucks sit idle, and materials arrive late.
2. Communication Gaps
Dispatchers, haulers, and job sites aren’t always on the same page. Schedules change, weather delays hit, or a customer suddenly needs more tonnage. If you’re still using group texts and phone calls to coordinate those changes, things fall through the cracks fast. And when they do, trucks wait, jobs stall, and the blame starts flying.
3. No Real-Time Visibility
If you can’t see where your trucks are or how many loads have been completed, you’re flying blind. You can’t fix what you can’t track. Many producers are left guessing:
- “Has that truck left the plant yet?”
- “Did that third-party hauler actually complete their shift?”
-
“How many more loads do we need before noon?”
That guesswork is expensive—and totally avoidable.
4. Repetitive Customer Inquiries
Every time a dispatcher stops to answer a “Where’s my load?” call, they lose time and focus. Multiply that by dozens of loads per day, and you’ve got a real drain on productivity. Customers want visibility, but without a better system in place, your team ends up playing middleman all day long.
5. Inaccurate Hauler Time Logs
Relying on drivers to record their own shift times or turn in paper tickets is a system built on trust—but not always on accuracy. Overpayments and disputes are common, especially when third-party haulers are involved. You need hard data to back up every hour worked.
Bottom line? These issues aren’t just annoyances—they’re the root cause of missed deadlines, lost revenue, and worn-out teams.
5 Ways to Cut Downtime and Keep Deliveries Moving
1. Smarter Dispatching Means Fewer Delays
Old-school dispatching methods can’t keep up with today’s pace. Trux replaces messy spreadsheets and phone chains with a simple, drag-and-drop interface. Assign jobs in seconds. Whether you’re managing your own trucks or pulling from your third-party pool, you can see who’s available and get them on the road—fast.
When plans change, just update the schedule with a few clicks. Haulers get notified instantly, so there’s no confusion about where to go, what to haul, or when to show up. That means fewer missed shifts and more completed loads.
2. Plan Your Loads Like a Pro
Guesswork doesn’t belong in a tight operation. Trux gives you visibility into exactly how many trucks you need, when you need them, and who’s currently active, idle, or unassigned. That makes it easier to plan ahead, avoid overbooking, and reduce delays between loads.
You can even factor in haul distances and turnaround times to fine-tune your daily targets.
The result? More material delivered per day. Less wasted time. A stronger bottom line.
3. Real-Time GPS Tracking—No Hardware, No Hassle
With Trux, you can track every hauler in real-time using GPS data straight from their phones. There’s no need to install expensive hardware or chase down third-party drivers for updates.
This live visibility lets you:
-
Spot delays before they become problems
-
Monitor traffic or route issues
-
Confirm that haulers are sticking to schedule
You’re not flying blind anymore. You’ll know where each load is at any point in the day—and your team can act fast when things slow down.
4. Let Customers Track Deliveries with the Delivery Tracker
How much time does your team waste answering the same question over and over again: “Where’s my load?”
With Trux’s Delivery Tracker, your customers get the answer themselves—no need to call. They can follow their deliveries on a live map (no app needed) and get real-time updates about truck location, ETA, and drop-off status.
That means:
-
Less back-and-forth with your dispatchers
-
Fewer delivery delays
-
Better-prepared job sites
And when deliveries run smoother, your customers are more likely to call you again next time they need material moved.
5. Validate Every Shift with Geofencing
Paper timecards and manual logs are a recipe for inaccuracy. Trux uses geofencing to track exactly when a hauler enters or leaves your plant, quarry, or job site. You get automatic, verified shift data—down to the minute.
No more:
-
Overpaying for idle time
-
Guessing when drivers showed up
-
Digging through paperwork to resolve payment disputes
With precise tracking, you’ll only pay for actual work performed—and your haulers will appreciate fast, accurate pay.
Trux Materials: Purpose-Built to Eliminate Downtime
Trux Materials isn’t just another dispatching tool. It’s a complete logistics platform designed specifically for material producers who are tired of delays, guesswork, and back-office clutter. Every feature is built around one goal: keep your operation moving at full speed.
Here’s how it works:
Centralized Dispatching That Works in Real Time
Forget juggling spreadsheets or re-sending updates every time something changes. Trux lets you assign and update hauler shifts in seconds, from one centralized dashboard. Whether you're using your own trucks or third-party haulers, everything happens in real time—no more delays, no more confusion.
Need to adjust schedules or reassign loads? It’s as easy as drag-and-drop. All haulers are automatically notified with the latest job details.
Live GPS Tracking for Every Truck—No Hardware Required
With GPS tracking built into the Trux mobile app, you’ll know exactly where every truck is at all times. That means:
- No more guessing if a truck is stuck in traffic or sitting idle
- No more waiting for check-in calls from haulers
- No need to install expensive tracking systems in your vehicles
This real-time data keeps dispatchers informed, job sites prepared, and customers confident that materials are on the way.
Delivery Tracker for Customer Self-Service
Your customers can view real-time updates on their deliveries without ever picking up the phone. The Trux Delivery Tracker gives them a live map of incoming trucks, ETAs, and delivery confirmations.
No app required. No login. Just a link they can click to track their loads. This cuts down on phone calls, reduces frustration, and builds trust through transparency.
Geofencing + Digital Shift Validation
With geofencing, Trux automatically tracks when trucks enter and leave key locations—plants, quarries, and job sites. That data is used to validate every shift, so you’re only paying for time actually worked.
No more time disputes. No more overages. Just accurate, defensible billing—especially critical when you’re working with third-party haulers.
Paperless Tickets and Summaries
Trux replaces messy paper load slips with digital tickets sent instantly from the job. Every load is recorded, time-stamped, and available for your back office in real time.
By the time a truck returns to the plant, your team already has the delivery on record—no scanning, no data entry, and no lost paperwork. You can even generate post-delivery summaries automatically, keeping your invoicing clean and fast.
Start Running Tighter, Smarter Hauls
Downtime happens when you don’t have the right information at the right time. Trux changes that. With more visibility, less manual work, and better communication across the board, you can take back control of your operation.
If you’re ready to deliver more material with less stress, let’s talk. Trux Materials is already helping producers move smarter every day—and we’d love to show you how.
Related Posts
Spring Construction Boom: How to Get the Most from Your Haulers When Demand Spikes
Spring marks the start of the busiest season for contractors and material producers. Demand for...
Top 5 Features to Look for in a Hauling and Delivery Management Platform
Managing material deliveries shouldn't be a constant headache. Between coordinating haulers,...
Digital Dispatching: The Future of Construction Fleet Management
Managing dump trucks has never been easy. Traditional dispatching methods—relying on phone calls,...