7 min read
Top 5 Features to Look for in a Hauling and Delivery Management Platform
By: TRUX Team on Feb 28, 2025 10:43:04 AM
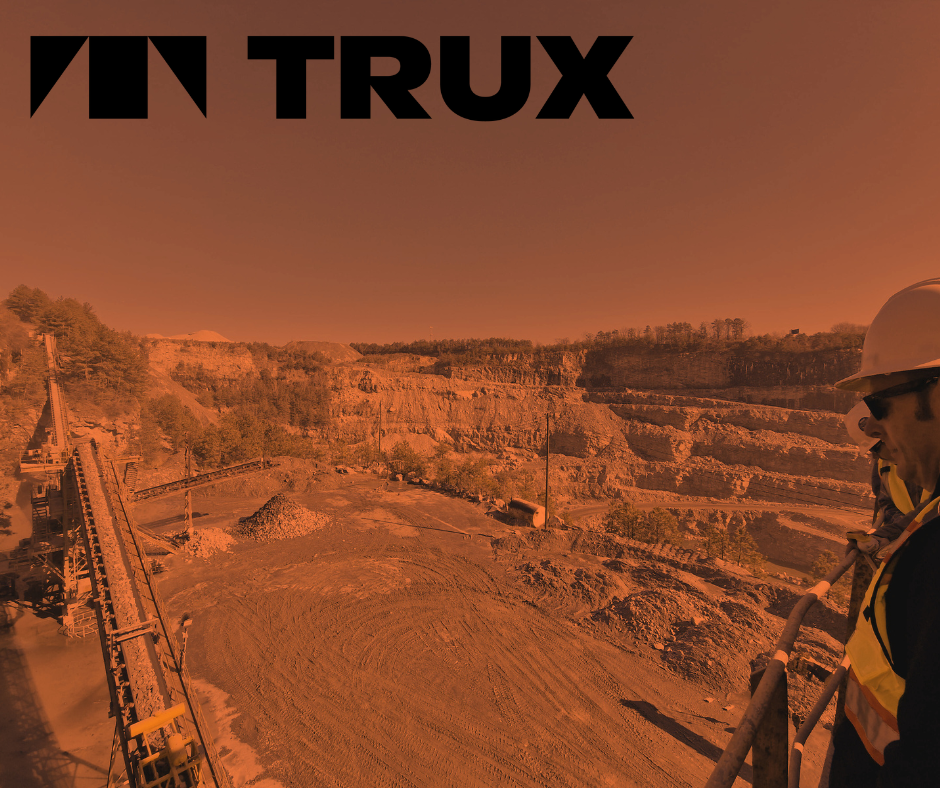
Managing material deliveries shouldn't be a constant headache. Between coordinating haulers, tracking deliveries, and ensuring accurate payments, there’s a lot that can go wrong. Missed loads, inefficient dispatching, and payment disputes can slow down operations and eat into your profits.
The right hauling and delivery management platform helps material producers take full control of their operations. By providing real-time visibility, streamlining dispatching, and automating key processes, a good platform ensures every load is accounted for from the plant to the job site—without the need for extra hardware.
However, not all hauling software is created equal. To make sure you’re investing in the best solution for your business, here are the top five must-have features to look for in a hauling and delivery management platform.
Click a topic below to jump to the relevant section:
1. Real-Time GPS Tracking for Full Visibility
2. Smarter Dispatching for Maximum Efficiency
3. Digital E-Ticketing & Paperless Documentation
4. Geofencing & Digital Shift Validation to Eliminate Overpayments
5. Plant & Quarry Optimization for Faster Turnaround Times
1. Real-Time GPS Tracking for Full Visibility
One of the biggest challenges in material delivery is not knowing where your trucks are at any given moment. Without real-time visibility, delays can pile up, job sites can be left waiting for materials, and dispatchers can waste valuable time making calls just to check on progress.
A hauling and delivery management platform with real-time GPS tracking eliminates this guesswork. With live tracking, you can monitor both company-owned and third-party haulers from the moment they leave the plant until they reach the job site.
How Real-Time Tracking Helps:
✅ See every truck in real time—know exactly where your loads are without needing extra hardware.
✅ Provide accurate ETAs to job sites, reducing downtime and keeping projects on schedule.
✅ Let customers track their own deliveries, cutting down on calls to your dispatch team.
✅ Identify bottlenecks at plants and job sites to improve turnaround times and avoid unnecessary delays.
A strong GPS tracking system ensures you always know where your haulers are and how efficiently materials are moving. This added visibility makes it easier to streamline dispatching, avoid costly delays, and improve customer communication—all key to running a smooth, profitable operation.
2. Smarter Dispatching for Maximum Efficiency
Efficient dispatching is the backbone of any successful hauling operation. When scheduling is done manually—through phone calls, texts, or spreadsheets—it’s easy for details to get lost, haulers to be double-booked, or jobs to be delayed. These inefficiencies can lead to higher costs, wasted time, and frustrated crews.
A modern hauling and delivery management platform simplifies dispatching with digital scheduling tools that allow for quick assignments and real-time adjustments. Whether managing your own fleet or third-party haulers, a streamlined dispatch system ensures that trucks are assigned faster and more accurately, reducing downtime and maximizing productivity.
How Smarter Dispatching Helps:
✅ Assign haulers quickly with a digital scheduling system—no more endless calls and texts.
✅ Adjust schedules in real-time, so when job details change, haulers are instantly notified.
✅ Ensure the right number of trucks are available, preventing under- or over-scheduling.
✅ Reduce dispatching errors that lead to delays, inefficiencies, and unnecessary costs.
With the right technology in place, dispatching becomes more than just assigning trucks—it becomes a proactive tool for optimizing daily operations, ensuring every load is delivered on time with minimal hassle.
3. Digital E-Ticketing & Paperless Documentation
For years, paper tickets have been the standard in hauling and material delivery—but they come with their fair share of headaches. Lost tickets, manual entry errors, and delayed invoicing can lead to payment disputes, back-office inefficiencies, and wasted time.
A hauling and delivery management platform with digital e-ticketing eliminates these issues by providing electronic records of every load in real time. This ensures that all stakeholders—dispatchers, haulers, and customers—have instant access to accurate delivery information, reducing confusion and improving efficiency.
How Digital E-Ticketing Helps:
✅ Eliminates lost or damaged paper tickets, ensuring every load is accurately recorded.
✅ Reduces billing errors and disputes with clear, digital documentation.
✅ Speeds up invoicing, getting payments processed faster and improving cash flow.
✅ Provides instant access to delivery records, improving transparency for haulers and customers.
Switching to a paperless ticketing system helps streamline operations, reduce administrative burdens, and create a more efficient and accurate payment process—ensuring you’re always paid for the work that’s been completed.
4. Geofencing & Digital Shift Validation to Eliminate Overpayments
One of the biggest concerns in hauling and material delivery is ensuring accurate payments for work completed. Relying on manual check-ins or self-reported hours can lead to overpayments, disputes, and unnecessary costs. Without a reliable system in place, you may be paying for time that wasn’t actually worked.
A hauling and delivery management platform with geofencing and digital shift validation solves this problem by automatically tracking when haulers arrive at and leave job sites, plants, or quarries. This eliminates guesswork and ensures payments are based on actual time on site—not estimates.
How Geofencing & Digital Shift Validation Helps:
✅ Automatically logs arrival and departure times, eliminating manual check-ins.
✅ Prevents overpayments by ensuring haulers are only paid for the time they’re actively working.
✅ Reduces disputes with clear, time-stamped records of every shift.
✅ Improves cost control, helping you manage budgets more effectively.
With automated shift validation, you get full control over hauler payments—eliminating unnecessary costs and ensuring accuracy every step of the way.
5. Plant & Quarry Optimization for Faster Turnaround Times
Efficient hauling isn’t just about getting materials to the job site—it starts at the plant or quarry. Long wait times, inefficient loading processes, and poorly timed dispatching can create bottlenecks that slow down operations, delay deliveries, and reduce the number of loads moved per day.
A hauling and delivery management platform with plant and quarry optimization tools helps material producers improve turnaround times by providing real-time data on truck movement, load tracking, and site efficiency. This allows dispatchers and plant managers to identify delays, adjust schedules, and keep operations running smoothly.
How Plant & Quarry Optimization Helps:
✅ Monitors inbound and outbound truck traffic to prevent congestion and delays.
✅ Tracks load times and wait times to identify inefficiencies and improve scheduling.
✅ Provides real-time ETAs, ensuring trucks are loaded and dispatched efficiently.
✅ Increases overall throughput, allowing more material to be delivered each day.
By optimizing plant and quarry operations, material producers can move more loads in less time, reduce idle time for haulers, and keep projects on schedule—all of which lead to a more efficient and profitable operation.
Conclusion
Choosing the right hauling and delivery management platform can make all the difference in running a more efficient and profitable operation. With the right features, you can track trucks in real-time, streamline dispatching, eliminate paperwork, prevent overpayments, and optimize plant operations—all while reducing costs and improving productivity.
By investing in a system that offers real-time GPS tracking, digital e-ticketing, automated shift validation, smarter dispatching, and plant optimization, material producers can take full control of their hauling operations and keep projects moving smoothly.
In today’s fast-paced industry, having the right technology isn’t just an advantage—it’s a necessity. If you’re looking for a way to simplify your operations and improve efficiency, it’s time to explore what a modern hauling management solution can do for your business.
Related Posts
Digital Dispatching: The Future of Construction Fleet Management
Managing dump trucks has never been easy. Traditional dispatching methods—relying on phone calls,...
Why It’s Time to Ditch Paper-Based Systems for Hauling Management
In construction, efficiency is everything. Whether you’re managing your own fleet or hiring...
Reducing Downtime: Best Practices for Hauling Operations
When your operation relies on steady material movement, downtime isn't just an inconvenience—it’s a...