6 min read
Why Last Mile Logistics is Critical for Heavy Civil Construction
By: Elizabeth Sholes on May 10, 2021 7:15:00 AM
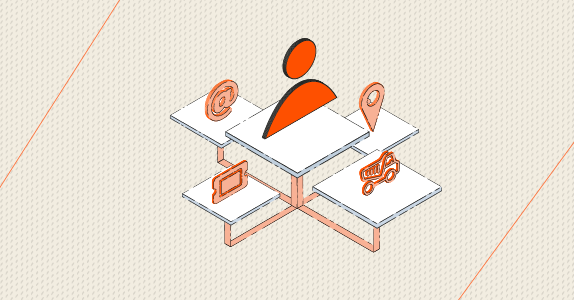
To get ahead, it’s time that heavy civil construction companies start focusing on last mile logistics. But one of the biggest problems in the heavy civil construction industry is that there really isn’t a separate and distinct component of the supply chain that’s defined as last mile. In the civil construction industry, it’s essentially all last mile.
So it’s easy for civil contractors and material producers to conduct business as usual with regards to their trucking logistics. They simply don’t recognize that the transportation part of their operations could be key to providing differentiated service that leads to profit gains.
“Last mile” isn’t really the last mile. It’s the last leg of the supply chain and can include distances up to 100 miles. Most dump trucks make trips on average of about 20 to 30 miles. With that in mind, the civil construction industry would be wise to view every mile as last mile and adopt the logistics best practices of the industry leaders in eCommerce.
In the conveyance of consumer goods from supplier to customer, there are basically three parts to a product’s journey:
- First mile--this is the origination point, the manufacturer or producer.
- Middle mile--this segment usually involves long-distance transportation and often includes shipments going through customs, port storage, preparation and loading for inland transport.
- Last mile--also called final mile, this is when the product is moved from a fulfillment center or local warehouse into the customer’s hands (or doorstep).
Of course, B2C companies have worked hard at achieving efficiency throughout all three legs of the supply chain. But in the last couple of years, last mile delivery has become the great differentiator for eCommerce. Think Amazon, Domino’s and other retail giants.
In our culture of gotta-have-it-now, these players have learned the importance of focusing their investments and energy into optimizing the last mile delivery phase. These days it’s not enough to have a superior product. If it arrives late or damaged or fails to arrive all together, the customer is likely to shop elsewhere. Today’s customer expects flawless delivery, or at the very least, timely updates on the status of their purchase. The delivery experience is part of the product.
It’s in this final step of the delivery process that companies can make a favorable impression on customers. They need to ensure the quality of their service is five-star to retain customers and gain their referrals.
Civil Construction Companies Can Learn Some Prime Lessons
There’s much to learn from the delivery innovators around the globe. When we look at those leading the competition in retail and distribution industries, we see two prevailing directives.
- Move toward technology.
- Move away from traditional logistics practices.
It can be reassuring to remember this: The top heavy civil construction companies are not necessarily the biggest firms. Rather, the successful companies are the ones who’ve realized the potential that lies between pick up and delivery and are using technology to reinvent their trucking logistics.
Last Mile Logistics Lesson 1: Increase Visibility with Real-Time GPS Tracking
From the jobsite foreman to the dispatcher, everyone involved in a heavy civil construction project can plan ahead and do their job more efficiently when they know what time to expect a truck to show up.
With real-time GPS tracking, dispatchers can instantly know the location of a truck and can communicate an accurate ETA to all parties involved. Crews can be readied for the task at hand. And arrivals to the jobsite can be staggered to prevent wasted time and fuel inefficiency due to trucks idling while waiting to unload.
Heavy traffic or road work is to blame for many delays which ultimately can result in a project getting off track in terms of budget and schedule. Dispatchers who are connected to their drivers through a trucking logistics platform can react quickly to events that will impact a trip. They can reroute to make up for lost time or send another truck if that’s a better solution.
In addition, construction jobsites come with their own set of small, but not insignificant, challenges. Jobsites often don’t have clear addresses. Navigating around the jobsite can be confusing and drivers aren’t always sure where to drop their loads. Then there are time-sensitive materials, like asphalt, that have a critical window for delivery time.
Even just a few instances of miscommunications from these situations can add up to costly delays and increased end-customer frustration. To circumvent these problems, many GPS tracking solutions also include a feature which allows drivers to receive specific instructions and continually be updated to changing conditions.
Last Mile Logistics Lesson 2: Boost Productivity with a Trucking Logistics Platform
Improved efficiency almost always translates into higher productivity for an organization. Many of the eCommerce leaders rely on third-party platforms that use cloud-based technology to ensure efficiency as well as productivity.
Civil construction companies that implement similar last mile logistics technology can realize the same gains. Through optimizing routes and more efficient scheduling, some TRUX customers have seen a 15% increase of loads per hour delivered.
In addition, the improved visibility into scheduling and streamlined dispatching means companies are positioned to increase the utilization of their fixed assets--like dump trucks--and eliminate deadhead mileage.
A trucking logistics platform creates time-savings for a number of other roles such as dispatchers and back office employees. It’s common for companies who have embraced digital solutions to experience as much as a 40% increase in productivity in these areas.
Last Mile Logistics Lesson 3: Optimize Operations with Digital Processes
The eCommerce leaders in last mile delivery dispensed with manual processes years ago. For optimal efficiency, scheduling and dispatching can be accomplished through software that simplifies the processes for civil construction, too. A schedule can be created, drivers can be dispatched and even change orders and bulk reorders can all be completed with just a few clicks.
Last mile logistics solutions with easy-to-use dashboards not only reduce the time it takes to create a schedule and fill it, but they shorten the learning curve of using the technology as well.
The ultimate in optimization is having the ability to handle your job from anywhere. Solutions that offer a mobile application make this possible. Scheduling and dispatching can easily be completed on the go.
The back office will also gain more time. Batching, invoicing and other manual tasks that normally would take hours (and are prone to error) are processed effortlessly, giving your employees more time to focus on revenue-generating activities.
Last Mile Logistics Lesson 4: Gain Insights with Logistics Data
The cost of delivery is often considered a line item. Without access to hard data it’s difficult to know how much spend is or how to effectively reduce costs. Last mile logistics changes all that. Every trip produces a goldmine of data that helps you monitor costs, reduce waste and price more efficiently.
With transactional records, data from individual delivery routes and data from individual vehicle movement, you can get a more precise picture of your overall logistics. Or, say one month you see an unusual uptick in spend, you can drill down into specifics to find out what happened and make adjustments.
The data collected through a logistics solution provides insights that you otherwise would not have.
Last Mile Logistics Lesson 5: Leverage Access to More Haulers
Granted, it’s easier for pizzas and packages to be delivered by a gig economy worker. But the lesson here is that you don’t have to own all the vehicles you need to improve last mile logistics.
Understandably, many suppliers in the construction industry have chosen not to provide delivery at all. The capital expenses and operating costs associated with owning and maintaining a fleet of trucks are high. Those expenses combined with the challenge of finding reliable drivers can make delivery services seem like a risky and unnecessary investment.
But those in heavy civil construction need to understand that last mile logistics is an area where you can gain a competitive edge. Offering this value-added service becomes viable when you consider using a network of third-party haulers.
TRUX has the nation’s largest network of technology-enabled dump trucks. But that’s just one piece of the TRUX solution.TRUX is a complete logistics platform for dump truck owners, contractors and material producers. With TRUX you can manage every truck you hire the same way you manage your own. And every load delivered is trackable--by both the material originator and the end-consumer.
With TRUX, every mile is last mile, so you get:
- More transparency to deliver to your customers
- Increased efficiency which leads to higher productivity
- Optimized processes to replace time-consuming manual tasks
- Useful data to gain insights and inform your decisions
- Easy access to a wide variety of dump trucks
What’s more, at TRUX we’re continually developing tools to help our customers get ahead. For example, delivery velocity visualization is now providing material producers with an accurate way to capture the number of tons per hour delivered while in the field.
If you want to learn more about the latest in last mile logistics for heavy civil construction, we’re always happy to talk about ways to transform your business. Give us a call.
Related Posts
Last Mile Logistics: Your Secret Weapon For Customer Service
Every successful business has its secret sauce. That thing that sets it apart from the others who...
How to Reduce Dump Truck Fuel Consumption | Fuel Efficiency Tips
Are you wondering how to reduce fuel consumption? Dump trucks require a lot of fuel to operate....
How Much Does a Dump Truck Cost? Operating Costs & Prices
As an owner operator, finding the optimal truck to suit your business needs is an important...